Reverse Engineering
Reverse engineering with a 3D laser scanner is the process of capturing the exact shape and dimensions of a physical object using laser scanning technology, and then using that data to recreate or analyze the object digitally—usually in CAD (Computer-Aided Design) software.

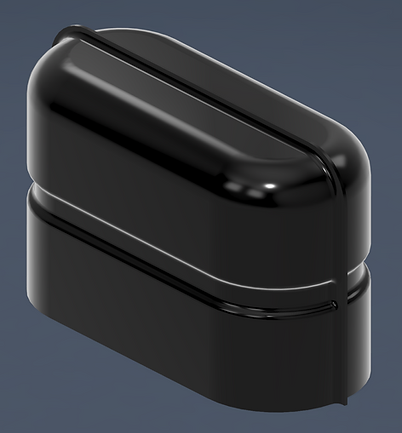
Scanning the Part/Assembly
A 3D laser scanner emits laser beams onto the surface of an object and measures the way the light reflects back. This process captures millions of data points—called a point cloud—that represent the surface geometry in high detail.
Creating a 3D Model
The point cloud data is converted into a mesh (often an STL file), and from there, engineers can create a solid CAD model. This model can be edited, measured, analyzed, or even modified for improvements.
Rebuilding or Modifying
Once the CAD model is complete, it's ready for:
-
Reproduction using 3D printing or CNC machining
-
Design modifications or improvements
-
Engineering analysis
-
Creating documentation or blueprints
Why use 3D laser scanning for reverse engineering?
-
Fast and accurate: Laser scanners capture precise details quickly, even on complex or organic shapes.
-
Non-contact: Great for fragile, worn, or valuable items—no need to physically disassemble or damage them.
-
Ideal for legacy parts: Perfect for situations where original CAD files or technical drawings no longer exist.
-
Saves time: Significantly faster than measuring manually.
This method is widely used in automotive, aerospace, product design, tooling, and especially 3D printing—because once the scanned model is ready, you can easily send it to a 3D printer for prototyping or final production.
Practical Applications of Reverse Engineering
Reverse engineering finds applications across various industries, breathing new life into products and components that would otherwise be obsolete. Here are some compelling examples:
-
Revitalizing Discontinued Electronics: Many companies reverse-engineer discontinued electronic components like printed circuit boards (PCBs) and connecting cards. These parts often belong to manufacturers that have shuttered their operations or ceased production of specific items.
-
Recreating Original Designs: In scenarios where the only way to access a product's original design is through reverse engineering, the technique becomes indispensable. Products that haven't been manufactured for decades can lack accessible 2D drawings or contact information for the original creators, necessitating reverse engineering to recover their designs.
-
Preserving Corporate Heritage: Companies sometimes revisit their own legacy products through reverse engineering. Consider a firm that's been around for several decades; it might have essential product designs documented only on paper blueprints, gathered long before digital storage was available. Reverse engineering helps these businesses digitize and archive historical designs, securing invaluable corporate heritage.
-
Revamping Classic Automotive Parts: Auto restoration frequently leverages reverse engineering to reconstruct vintage engine and body components. Car collectors and restoration experts use this approach to reproduce rare parts, allowing classic cars to roar back to life without altering their fundamental design.
These examples show how reverse engineering is crucial in maintaining, restoring, and preserving technology and products that might otherwise fade into obscurity.
The Role of Reverse Engineering in Failure Analysis
Reverse engineering plays a crucial role in the process of failure analysis by offering a systematic approach to uncovering the root causes behind a machine or product failure. When a machine breaks down, pinpointing the exact reason can be challenging. This is where reverse engineering steps in to provide clarity.
Investigating the Problem
By disassembling the machine and scrutinizing every component, reverse engineering allows for a comprehensive investigation. This involves examining each part for wear and tear or potential manufacturing defects that might have contributed to the failure.
Design File Inspection
In addition to physical inspection, reverse engineering also extends to the analysis of digital design files. These files, which map out the machine's original design, can highlight any discrepancies or design flaws that are not immediately visible through physical examination.
Informing Repairs and Improvements
Armed with insights from both physical and digital evaluations, reverse engineering informs strategic plans for repairing the machine. Moreover, it opens up opportunities for refining the design, thereby improving functionality and preventing future failures.
Enhancing Product Longevity
Ultimately, reverse engineering enhances the overall functionality and durability of a product. By identifying defective parts or design faults, it helps ensure that the product not only returns to working order but does so with longer-lasting performance.
In summary, reverse engineering serves as a detective tool in failure analysis, converting breakdown mysteries into knowledge, which is then used to drive repair and innovation.
Reverse Engineering for Parts Service or Repair
Reverse engineering plays a vital role when dealing with parts that are no longer supported by the Original Equipment Manufacturer (OEM). Here's how it can be effectively utilized:
-
Understanding Unavailable Parts: When encountering a legacy part that lacks support or documentation, gaining insight into its function becomes crucial. Reverse engineering helps in deciphering the inner workings of these components, providing necessary information even when original design documents are missing.
-
Creating Design Documents: By reconstructing the product's design, reverse engineering allows companies to generate new design documents. This becomes particularly useful in the absence of original blueprints, enabling technicians to better understand the product's structure and functionality.
-
Informing Repair Techniques: The information gleaned from reverse engineering guides the repair process. By identifying faulty components, technicians can strategize the replacement process, ensuring repairs are both accurate and efficient.
-
Optimizing Component Access: With a clearer understanding of the product’s assembly, reverse engineering aids in determining the best approach to access, remove, and replace specific parts, thereby streamlining the repair operation.
Reverse Engineering serves as a critical tool in the maintenance and repair of obsolete or unsupported parts, helping technicians revive what would otherwise remain unsalvageable. By piecing together the product's details, it not only solves immediate repair challenges but also extends the life of valuable equipment.
Testing and Prototyping Importance in Reverse Engineering
In the world of reverse engineering, testing and prototyping are crucial for multiple reasons:
Validating Design Assumptions
When you reverse engineer a product, the initial step often involves creating a digital model. However, this theoretical construct needs physical validation. Testing and prototyping allow engineers to confirm or refute their design assumptions effectively, bridging the gap between the digital and physical realms. Without this step, the risk of basing your final product on incorrect assumptions can significantly increase.
Identifying Hidden Issues
Digitally modeled designs can sometimes overlook physical challenges or unexpected issues that only become visible when a prototype is created. Engaging in hands-on testing uncovers these unforeseen problems, enabling you to address them before full-scale production. This process is essential to refine your design and negate potential errors that could lead to costly recalls or redesigns later down the line.
Facilitating Necessary Improvements
Prototyping not only reveals existing issues but also opens the door for improvements. Testing a physical model provides insights that can be leveraged to enhance functionality, efficiency, and user experience. Each iteration gives invaluable feedback, driving innovation and ensuring that the final product is optimized in every way possible.
Reverse engineering is not solely about deconstruction; it's a process that thrives on careful analysis and iteration. Testing and prototyping serve as the backbone of this process, ensuring that every design choice is tested and optimized for real-world application, thereby enhancing overall product reliability and performance.

Get in Touch
Want to learn more about Reverse Engineering or have a product that needs to be scanned? Contact Us for help!