The Pros and Cons of 3D Printing with TPU: Why It's a Game-Changer for Product Development
- Brad Harbert
- 2 days ago
- 3 min read
At Outlaw Prototyping, we work with a variety of materials to help clients across industries bring their product ideas to life. One material that often catches the attention of forward-thinking engineering leaders is TPU, or thermoplastic polyurethane. Known for its flexibility, durability, and chemical resistance, TPU has emerged as a popular choice for functional prototyping and even end-use parts. But like any material, it comes with its pros and cons.
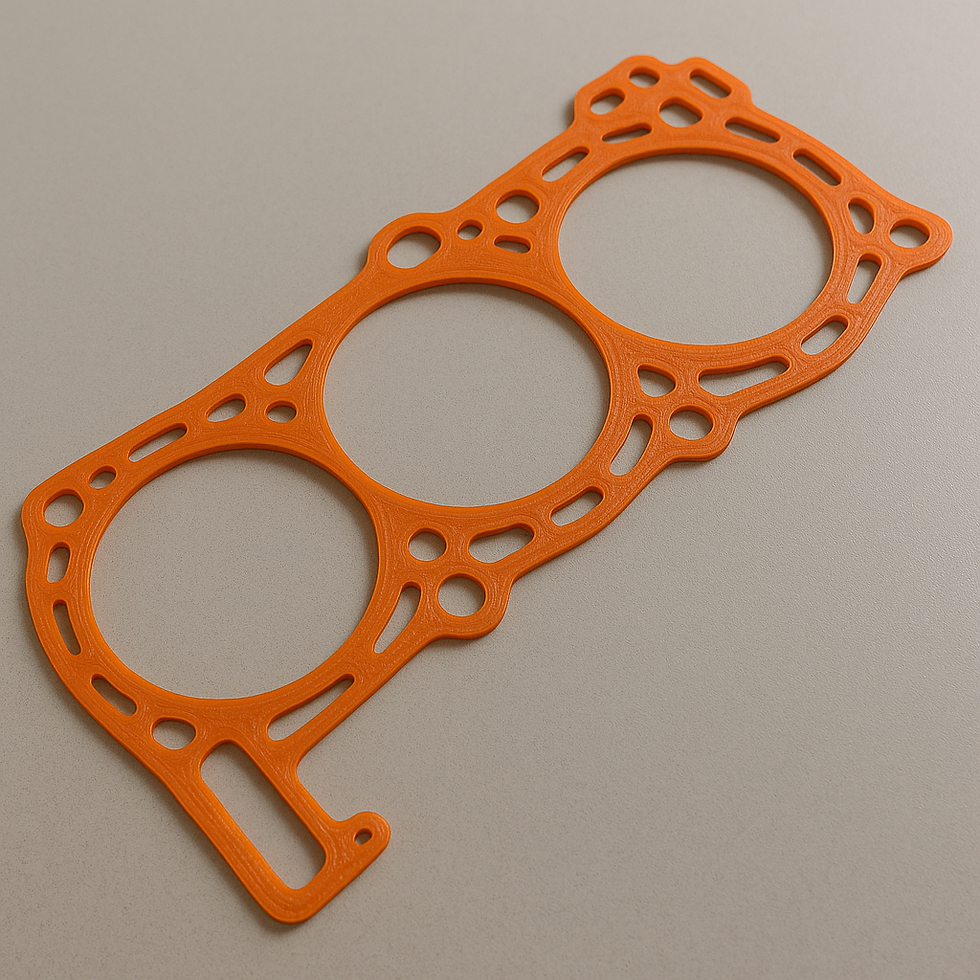
This post will walk you through the benefits and limitations of TPU in 3D printing and include a couple of case studies that demonstrate how companies have successfully leveraged TPU to optimize their product development and manufacturing workflows.
What is TPU?
TPU is a class of thermoplastics known for its elasticity, transparency, and resistance to oil, grease, and abrasion. In the world of 3D printing, TPU is typically used in FDM (fused deposition modeling) or SLS (selective laser sintering) printers to create flexible, durable parts.
Benefits of 3D Printing with TPU
Flexibility and Elasticity
TPU behaves more like rubber than a traditional plastic. This makes it ideal for creating components that need to flex or compress without breaking, such as gaskets, seals, insoles, and protective casings.
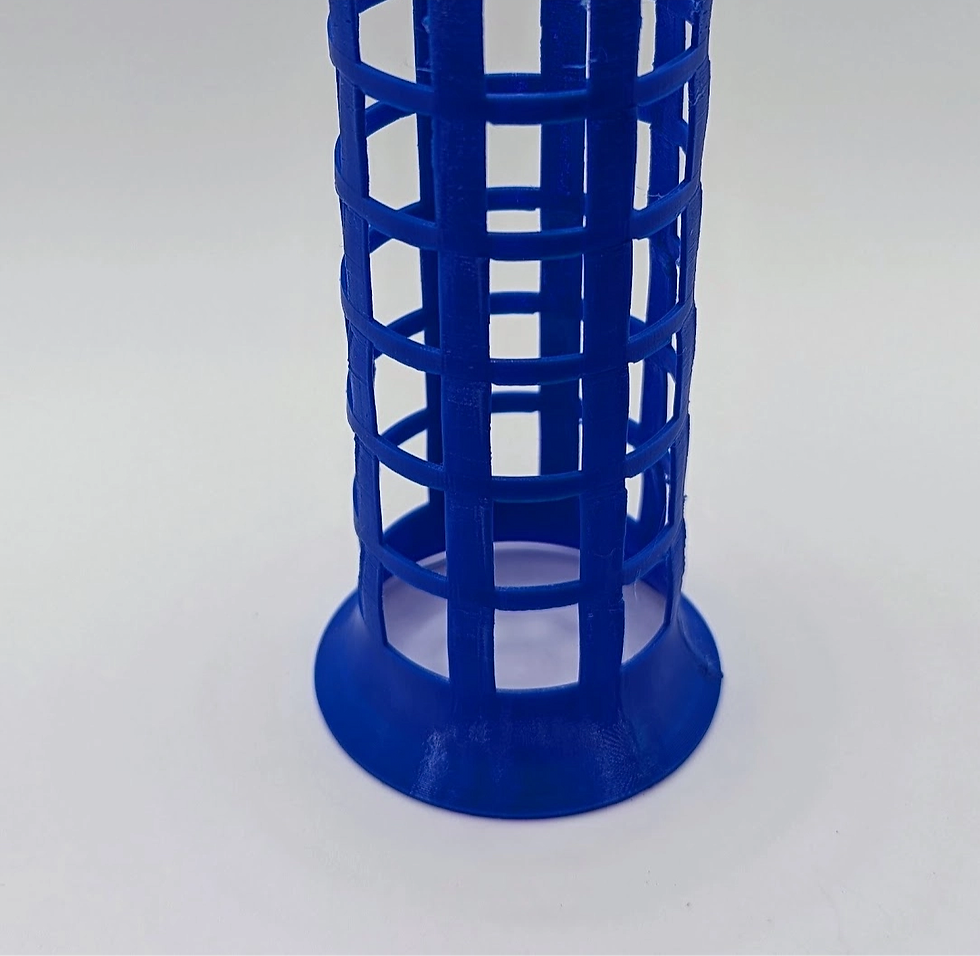
Durability and Abrasion Resistance
TPU can take a beating. Its high resistance to abrasion and impact makes it suitable for parts that experience wear and tear. It also maintains its integrity over time, even in rough environments.
Chemical and Environmental Resistance
TPU resists oils, greases, and a variety of chemicals, making it a great choice for parts used in automotive, industrial, or medical settings. It also holds up well in a range of temperatures and weather conditions.
Shorter Product Development Cycles
Because of its mechanical properties, TPU allows for functional prototyping early in the development process. Engineers can test designs under realistic conditions and iterate quickly.
Low-Volume Production Ready
With 3D printing, TPU can be used for small-batch production without the need for expensive molds. This is especially beneficial for startups or companies producing niche or custom products.
Drawbacks of 3D Printing with TPU
Printing Difficulty
TPU's flexibility, while beneficial in the final part, can make it difficult to print. It tends to string, warp, and jam more easily than rigid filaments. Successful TPU printing requires a finely tuned machine and operator experience.
Longer Print Times
Due to the slower print speeds required to avoid filament binding and improve quality, TPU prints can take significantly longer than those made with PLA or ABS.
Dimensional Accuracy
Achieving tight tolerances with TPU can be tricky. Its flexibility means that parts can deform slightly during the printing or post-processing stages, affecting precision.
Post-Processing Challenges
Supports can be harder to remove, and sanding or finishing flexible materials is more complex than with rigid plastics. Design for manufacturability is especially important when using TPU.
Case Study: Industrial Equipment Manufacturer Reduces Downtime
A manufacturer of custom industrial equipment came to Outlaw Prototyping needing replacement cable grommets for legacy machinery. The original supplier was no longer in business, and creating new molds would have been costly and time-consuming.
Using TPU, we reverse-engineered the grommets and began printing replacements within a week. The printed grommets matched the required mechanical properties and performed well under high-vibration and oily conditions.
The manufacturer was able to resume production faster than expected and decided to keep a digital inventory of these parts for on-demand 3D printing, streamlining their maintenance workflow going forward.
Conclusion: When to Choose TPU for Your Next Project
TPU is a versatile material that bridges the gap between rigid plastics and elastomers. While it requires some finesse to print, the advantages it offers in terms of flexibility, resilience, and speed to market make it a valuable tool in any engineering team's toolkit.
At Outlaw Prototyping, we’ve helped companies of all sizes integrate TPU into their design and manufacturing strategies. Whether you’re developing a new product or maintaining existing systems, TPU could be the flexible solution you’re looking for.
If you’re curious about how TPU can work in your specific application, reach out to our team. We’re always ready to help you explore the possibilities of additive manufacturing.
Comments